Our Solutions
KPA EtherCAT Master
KPA EtherCAT Master is a software stack, which corresponds to all EtherCAT Technology Group stan-dards and has numerous features, which can be used for developing of cost-optimized and powerful PLC on almost any platform (such as arm/arm64 or x86/x64) to control EtherCAT I/O produced by any vendor.
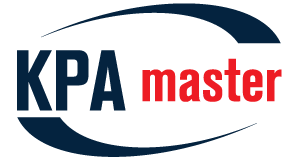
KPA EtherCAT Master is a comprehensive product for industrial automation specialists who intend to add high-speed communication capabilities to their applications and solutions. It is a second generation of EtherCAT Master by koenig-pa, implementing a new advanced architecture and several unique features that facilitate better integration and performance increase. Also, it supports a various range of operating systems.
Benefits and key features
- Meets EtherCAT Technology Group (ETG) standards
KPA EtherCAT Master can be delivered as standard or customized feature packages. Two standard packages are available according ETG.1500 standard: Class A (Standard package) and Class B (Basic package). Moreover, koenig-pa GmbH introduces Premium package, which integrates various additional features for creating innovative applications. - Available for numerous operating systems, as well as OS-less systems
KPA EtherCAT Master is available for numerous operating systems, including Windows, INtime, RTX/RTX64, Linux, Linux+Xenomai, FreeRTOS, Nucleus, QNX, VxWorks, ReWorks, Integrity, as well as OS-less systems. Upon request, koenig-pa GmbH experts can adjust support for any operating system. - Hardware extensions for Xilinx/Intel FPGA (Altera) and Texas Instruments PRUSS Sitara CPU
Availability of IP Cores for Xilinx and for Intel FPGA (Altera) FPGAs, PRUss co-program for Texas Instrument Sitara CPUs (AM47x and AM57x) increases productivity and data processing efficiency. - Auto Configurator for online configuration
KPA EtherCAT Master can configure bus on the fly without EtherCAT configuration tools. The Auto Configurator module allows a user application to select slave’s configuration and to switch between different configurations of the slave, for example, between position control of a drive and velocity control, or between bus configurations with a different number of slaves. - Process image logging for data transferring into analytic tools
Process image (PI) logger allows to collect real-time data for transferring to other levels without influence on real-time behavior of the control system. Data can be transferred to MATLAB, LabView (TDMS format), and any other analytic tools. Moreover, koenig-pa GmbH has designed a special Python extension, which allows to aggregate data into a file of any format, for example a CSV-file, for its further processing.
From Our Solutions
SAS Production Monitoring System
We monitor the production in real-time, delivering data for immediate reaction. The actual operation time of..
Read moreCustomize Report Solution
Operators report execution of works by using dedicated visualisations available in the browser..
Read moreMobile App Solutions
It needs a system that is always within reach, which would contain the most current data regarding failures..
Read moreSAS Quality Control
SAS a system which provides information about exact location of each product. The greatest added value..
Read moreReal-Time Solutions
Production planning is the key area of optimisation of production and minimising down times..
Read moreEnergy Monitoring System
The system provides monitoring of consumption of a production plant. Ensures connection of..
Read more